Energy Challenges are Rising. Here’s How Manufacturers Can Remain Competitive
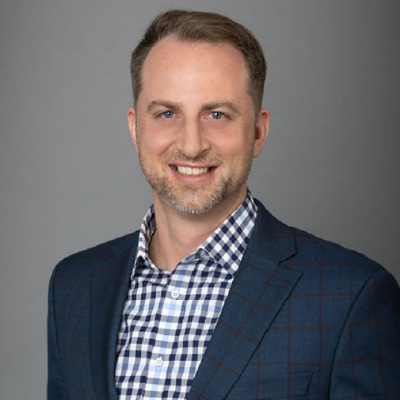
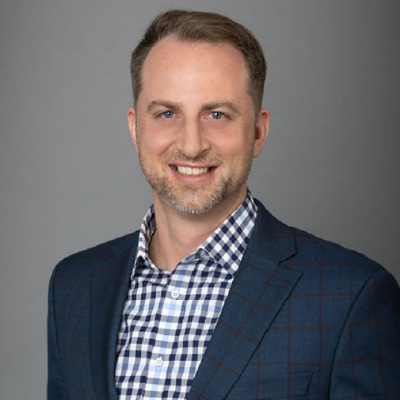
Industrial manufacturers nowadays face a perfect storm of challenges – rising energy costs, more frequent climate disruptions, and growing market volatility. These factors are forcing manufacturers to reconsider their energy strategies, with an increasing need for more sophisticated sustainable energy practices and enhanced resilience. As energy expenses now represent a growing share of production costs, manufacturers can no longer afford to treat energy bills as a fixed or predictable cost. For example, many industrial companies today are unaware that a large percent of their bill is likely hefty demand or coincident demand (COIN) charges, often costing an order of magnitude more than off-peak usage, let alone what they can do about it.
Further compounding these challenges are climate change, cyberattacks, and fluctuating energy markets, which have created an operational landscape defined by constant uncertainty. Predictable energy bills are no longer guaranteed, with many utilities forecasting double-digit price increases over the coming decades1. At the same time, sustainability has become an equally pressing concern as consumers demand eco-friendly products, and regulators enforce stricter environmental standards.
The bottom line: How manufacturers think about energy has evolved from being a most tactical concern to a strategic imperative. Rising energy costs and the increasing demand for sustainable manufacturing have transformed energy strategy from a secondary consideration to a top business priority. Manufacturers can no longer afford to stand still, but how many are truly prepared for what lies ahead?
A New Approach
To address these challenges, manufacturers must gather more granular data and implement solutions that deliver financial, operational, and environmental value. This includes deploying adaptable systems that can withstand disruptions and recover quickly, while understanding current energy consumption in detail and leveraging advanced technologies to integrate both conventional and renewable energy sources.
With energy expenses now representing a substantial portion of production costs, traditional “pay-and-forget” approaches have become increasingly untenable. To stay competitive, manufacturers must adopt dynamic energy management strategies that allow for real-time adjustments and long-term optimization. Granular descriptive insights into energy usage—coupled with predictive analytics—enable manufacturers to manage costs more effectively while improving energy efficiency across their operations. Artificial intelligence (AI) and AI agents offer new opportunities to take this even further, with prescriptive insights and automation of process and scheduling optimization strategies.
These tools not only curb costs but also optimize facility and equipment-level energy usage, enabling predictive maintenance, reduced downtime, and consistent production quality. Enhanced visibility into energy supply and demand—spanning shop-floor equipment, processes, and schedules—is critical to uncovering inefficiencies, risks, and opportunities for improvement. It also enables choices about when to produce products with the highest energy requirements, for lower costs or lower carbon intensity of the power coming in from their utility. Imagine component manufacturers being able to share granular energy and embedded carbon insights with their product manufacturing customers, who are struggling to report on their supply chain sustainability today.
Protecting operations during disruptions is also top priority. Investing in energy-resilient infrastructure, such as microgrids powered by solar, wind, and battery storage, ensures continuity during grid failures. Such systems stabilize energy supply and support cost-saving strategies like peak shaving and load shifting, making operations more reliable and efficient.
Manufacturers must integrate renewable energy systems and adopt AI-powered tools to meet these demands. AI can optimize energy management by analyzing real-time data, improving decision-making, and enhancing operational efficiency. Advanced analytics provide actionable insights into energy usage and carbon footprints, enabling facilities to lower emissions, improve profitability, and achieve regulatory compliance. AI agents, Large language models (LLMs) and automation can help people on the shop floor make the right decisions, focus on the nuances that humans are good at, and understand the tradeoffs in scheduling and production choices from the perspectives of economic, operational, and environmental value.
Many decisions on a manufacturing site remain siloed today. But a systems-based approach that balances cost management, resilience, and sustainability is critical for manufacturers to thrive. Enhanced visibility into both energy supply dynamics and demand patterns uncovers inefficiencies, risks, and opportunities for improvement. Technologies such as Internet of Things (IoT) sensors, energy storage systems, and AI-driven tools allow manufacturers to shift energy consumption to lower-cost periods, lower-carbon times of day, reduce peak demand charges, and optimize operations.
Proactive energy management can help manufacturers anticipate future cost increases, address operational risks, and meet sustainability goals. By strategically preparing for energy disruptions, manufacturers can position themselves for long-term success. Those who embrace these strategies will not only secure a competitive edge but also contribute to a sustainable industrial future.
Preparing for the Unexpected
While cost reduction and sustainability often dominate the conversation, energy resilience must be part of any strategy. That’s because natural disasters, intensified by climate change, are occurring with greater frequency and severity, placing unprecedented strain on energy grids and infrastructure. Hurricanes, floods, and wildfires are no longer rare events but annual threats that jeopardize facility operations and business continuity. Not only that, but insuring real estate and assets in disaster-prone areas is becoming increasingly expensive and uncertain, but resiliency infrastructure and data-driven continuity plans can help reduce risks, lost revenue, and recovery costs.
Additionally, cyberattacks have become more common and more sophisticated. These attacks can disrupt power delivery, compromise safety, and lead to costly operational downtime. Market volatility further complicates the picture, as fluctuating energy prices and regulatory decarbonization mandates create uncertainty in long-term planning.
To mitigate these risks, energy resilience strategies should include the integration of microgrids, renewable energy systems, intelligent digital energy management systems, and energy storage solutions. These systems provide a localized and self-sufficient energy supply, ensuring business continuity during grid failures or extreme weather events.
A Strategic Path Forward
Manufacturers who want to stay ahead of rising energy costs and meet sustainability goals must take a strategic, comprehensive approach to energy management, beginning with gaining visibility into energy consumption within their factory walls, using intelligent tools to understand what to do about it, and culminating in the implementation of robust, integrated infrastructure that enables smarter decision-making about how and when energy is used.
The foundation of effective energy management lies in conducting comprehensive energy assessments. Mapping energy flows across a facility reveals inefficiencies, high-cost processes and interdependencies. These insights enable organizations to prioritize cost-saving opportunities while advancing sustainability initiatives.
Digital solutions are central to engineering this transformation. By deploying sensors and analytics, businesses can achieve more granular real-time monitoring of facilities, equipment, and processes, while AI-powered recommendations optimize daily operations to enhance cost efficiency and minimize emissions.
AI-powered tools can also help manufacturers proactively address energy and carbon-saving opportunities and identify maintenance needs, preventing disruptions before they occur. Proactive recommendations help prevent costly repairs and unplanned disruptions, ensuring smoother operations. Additionally, IoT and advanced analytics offer real-time visibility into energy usage, allowing facilities to anticipate grid fluctuations, optimize energy distribution, and align operations with the most cost-effective energy sources.
Renewable energy systems and advanced storage solutions also play a key role in diversifying energy supplies. By integrating solar, wind, and battery technologies, businesses can reduce dependence on external grids, mitigate exposure to price volatility, and minimize their environmental impact.
To complement these efforts, microgrids provide localized energy networks that can function independently or in tandem with the main grid. These systems ensure a continuous power supply during outages while maintaining an effective balance between cost efficiency and sustainability.
Strategic Partnerships: A Roadmap to Success
Navigating the complexities of energy optimization demands both expertise and collaboration. Here’s where trusted partners like Hitachi can offer AI-powered solutions that empower industrial leaders to anticipate disruptions, optimize energy usage, reduce costs and emissions, and strengthen operational continuity.
By integrating granular facility-level data with broad supply-side insights, Hitachi helps businesses achieve cost reductions that were previously unavailable to them. With its comprehensive solutions, Hitachi also enables manufacturers to improve sustainability while building resilience against future challenges.
To explore how Hitachi’s advanced tools and technologies can help your facility achieve energy efficiency and resilience while remaining agile in an ever-changing environment, click here.
1 2025 Power and Utilities Industry Outlook, Deloitte, https://www2.deloitte.com/us/en/insights/industry/power-and-utilities/power-and-utilities-industry-outlook.html
Justin Bean
Sr. Manager of Business Development and Strategy, Hitachi Environment Business Division – North America
Justin furthers the mission of social innovation and building a more sustainable society through technology and business innovation. He incubates solutions and new businesses to support sustainable, circular economy as part of Hitachi’s Environment Business Division. Justin has worked with both Silicon Valley startups and fortune 500s that are applying AI, IoT, and other disruptive technologies to improve our cities, commutes, and daily lives. He has worked in the US, Japan, and South Africa on projects that include smart cities, smart parking, electric vehicles, renewable energy, machine learning, and 3D printing. Justin was the recipient of the THINK Prize for the Financial Empowerment Challenge from renowned innovation and design firm IDEO and holds an MBA in sustainable management.
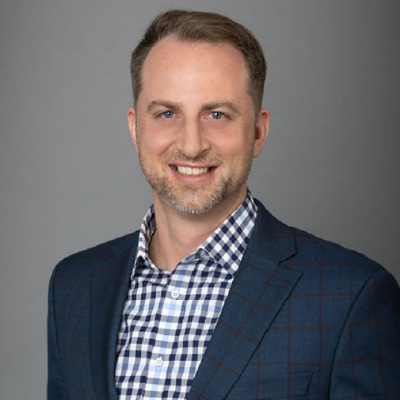
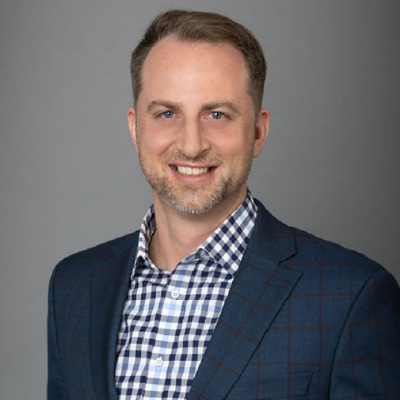